PLANTE BATTERIES
PLANTE BATTERIES
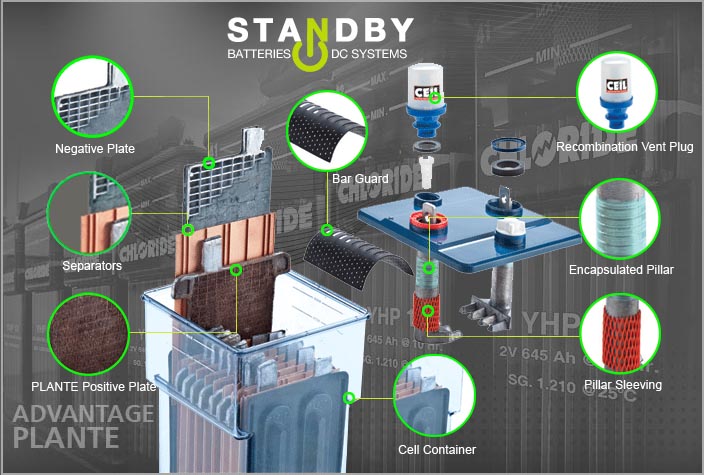
The INSIDE Story
The Plante Battery was designed in 1859, and till to today, it is still widely used in the Industries such as Power Generation, Transmission & Distribution, Oil & Gas, Telecom, etc., due to its reliability and long life.
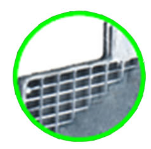
Negative Plate
The negative plates are cast in antimony grid, and pasted with lead oxide using state of the art MAC (US) pasting machine which ensure uniform density and texture. This helps to enhance the longevity of the battery.
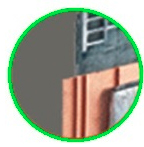
Separators
DARAK-5000 microporous duroplastic separator. It has high temperature stability, mechanical strength, low electrical resistance, high porosity and low acid displacement which makes it very efficient.
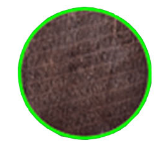
PLANTE Positive Plate
The reliability and long life characteristics of the Plante battery lie in its positive plates being :
The Positive Plate is casted with 99.99% pure lead, which helps to prevent corrosion and reduces the topping-up frequency significantly, thus less maintenance.
The grid thickness is over 8mm, which gives the Plante battery the highest longevity among all other batteries.
Its lamellar grid design give its apparent surface area 12 times its size, resulting in its high discharge performance.
The active material on the Positive Plates are self-generated, and re-generated throughout its lifetime, thus, there is no loss in capacity, and always remain at 100% capacity, unlike the rest of the industrial batteries whose end of life capacity degrade to 80%.
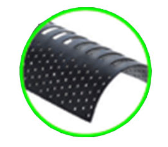
Bar Guard
This rubber material helps to safe guard against any debris discharge from the scaling of the group bar, and this debris deposit can be taken out or flushed put during routine maintenance with a suction pump.
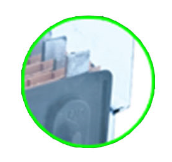
Cell Container
The cell container is made from the Styrene Acrylonitrile (SAN) material, and it is fully transparent, thus, it gives the advantage of the visual aid to detect early sign of problem.
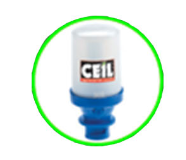
Recombination Vent Plug
The cylindrical design recombination element in the plug is filled with catalytic element and absorption deposit. During charging of the battery, oxygen and hydrogen gases will evolve. As these gases pass through the adsorption deposit, the catalytic element within the deposit will get heated up, thus, causes condensation on the inner plastic wall of the Recombination Vent Plug. This droplet of water will then trickle back into the cell, thus, it can help extend the topping up period by at least 5 to 10 years.
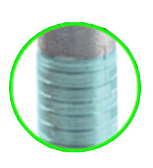
Encapsulated Pillar
The pillar is specially constructed using an injection moulded polymer encapsulation around it. The ribbed design of the pillar at the point of the scaling totally eliminate the Crevice Corrosion cause by acid seepage between the rubber gasket and post pillar.
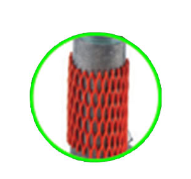
Pillar Sleeving
The pillar sleeving helps to encompass any scaling debris from falling off the pillar, which may cause shorting of the group bars or plates, thus, its preventive measure promotes longevity of the cell.